Validation Master Plan
A Validation Master Plan, or VMP, is a high-level document that details what, how, and when validation activities will be executed. It also identifies the validation approach, responsibilities, and documentation required to ensure that quality standards and Good Manufacturing Practices (GMP) (i.e. Good Clinical Practices, including current Good Clinical Practices or cGCP) are met. In addition, a Validation Master Plan gives an overall picture of how GMP has been integrated and illustrates how disparate validation activities are organized and inter-linked.
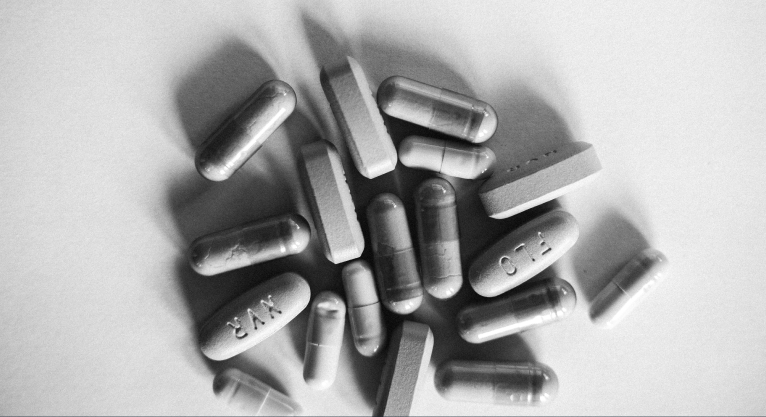
Occasions that warrant a Validation Master Plan are when new product manufacturing is being set up or when significant changes are made to product development processes, facilities, or equipment that could impact product quality. In these cases, a master validation plan should be developed in advance of beginning validation activities.
Since a Validation Master Plan is not a U.S. Food and Drug Administration (FDA) requirement, there is no mandated format for it. However, there is an expectation that a Validation Master Plan would be available for review during an audit.
Validation Defined in Terms of GMP Validation is the collection and evaluation of data, from the design stage through production, that is used to provide trustworthy evidence that a process and or device can consistently meet quality standards. |
Let’s jump in and learn:
What Is a VMP?
A Validation Master Plan summarizes all required people, systems equipment, timing, and processes. The plan should also reference all applicable protocols and reports related to each included item.
The plan should detail any revalidation requirements with notes about when the last validation was performed and the recommended frequency of revalidation. In some cases, the rationale or triggers for validation or revalidation are included in the plan.
Once the execution of the Validation Master Plan has been completed, a report should be created. This report should confirm that all validation activities have confirmed satisfactory results. It should also include a summary of activities undertaken, the overall conclusion, and references and links to any associated reports or follow-up actions.
Validation Master Plan Functions
Create the Validation Master Plan concurrently with manufacturing design and development efforts. It represents the lifecycle of the manufacturing validation process.
The Validation Master Plan functions as a roadmap for strategy and planning work as well as a framework for GMP documentation requirements, including process validation, facilities, utility qualifications, equipment qualification, cleaning, and computer validation. Among the many functions of a Validation Master Plan are the following.
25 Validation Master Plan Functions
1. Acts as a centralized index about each validation status
2. Controls and defines the different parts of the production process to ensure that production will not substantially change over time
3. Directs instrument validation strategy
4. Documents programs, including the scope of the validation effort (e.g., impacted product, procedures, processes, equipment, facilities, utility systems)
5. Eliminates ambiguity in justifying validation activities—internally within teams and externally for inspectors and auditors
6. Enables stakeholders to agree on the details of the validation strategy
7. Ensures that a specific piece of equipment or process performs as expected
8. Explains the validation rationale associated with the installation, start-up, and use of production lines
9. Facilitates agreement on and documentation of an overall process
10. Gathers key input from various stakeholders into the scheduling of project timelines
11. Identifies anticipated resource needs
12. Includes a schedule that identifies specific timetables for when each validation will take place and by whom—note that the quality team controls validation activities and defines the impacted functional areas in the document
13. Informs and educates senior management about the importance of validation in terms of its downstream impact on product quality
14. Justifies the strategy
15. Keeps the organization in a continuous state of validation
16. Lists the systems and equipment that must be validated and validation processes for each
17. Mitigates risks to the product manufacturing or consumers
18. Outlines the preliminary test and acceptance criteria
19. Provides the ability to demonstrate which validation activities are in process or pending execution
20. Reduces the risk of red flags and errors coming up in an audit
21. Reviews manufacturing systems and assesses the potential of each to negatively affect quality
22. Serves as a map with the logistic rationale for the next validation steps and efforts
23. Sets the course for validation work
24. Supports management of multiple validation documents and activities
25. Perhaps the most valuable of the Validation Master Plan functions is providing the documentation that regulators require during an audit. The Validation Master Plan illustrates the level of control over quality and compliance with GMP.
In the event of an unexpected audit, before all validations have been completed, the Validation Master Plan will help demonstrate the due diligence and intention to comply with the requirements.
Critical Components of a VMP
Although the Validation Master Plan is not a mandated document, FDA auditors ask for it, because it should give them an overview of the organization’s approach to validation, including them how responsibilities are assigned as related to:
- Plans for allocating and utilizing resources
- Product design processes
- Programs to establish and maintain a fully-trained, competent workforce—along with proof of ongoing training and confirmation that standards are met
The Validation Master Plan should also describe the scope of the activities and address relevant key elements of validation that could impact product quality. Recommendations for what to include in the Validation Master Plan are as follows.
- Title, statement of commitment, and title page
- Statement of the organization’s validation policy
- Summary of the project and its scope
- Objectives of prospective, concurrent, and retrospective validation activity
- Plan for documentation management and control system to be used
- Description of the validation change management process
- Clear acceptance criteria against which the outcome of the validation exercise will be judged
- Time, location, priority, and order of validation activities
- Details of personnel or facility management responsible for the approved the plan
- List of staff members who are accountable and provide approval for:
- Standard operating procedures or SOPs and quality protocols
- Review and maintenance of reference tracking systems
- Plans for validation training programs
- Overview of scope of operations that includes a description of facilities, systems (i.e., process equipment and services including automated systems), materials, quality controls, and products
- Summary of hardware, software, associated equipment, instrumentation, and documentation (e.g., manuals, SOPs)
- Facility description, such as:
- New construction, extension, or remodeling of an existing building
- Facility characteristics (e.g., number of floors, the inter-connectivity of process and utility systems, isolation means)
- Process flow diagrams (PFDs) to illustrate how cross-contamination will be minimized, including the flows of personnel, raw materials, processes, and waste
- Room classification, such as cleanroom certification levels or specialty surfaces and finishes integral to achieving the required product quality
- Selection criteria for which equipment and systems will undergo commissioning and qualification
- References to other existing validation documents
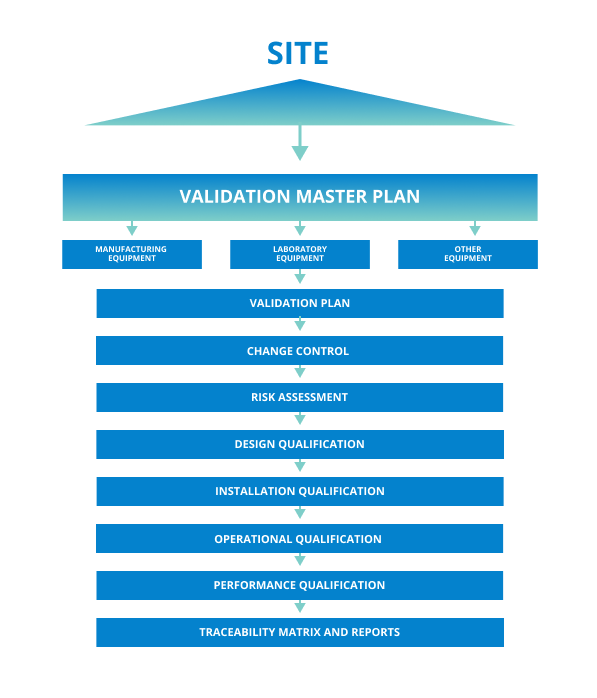
Tips for Writing a Validation Master Plan
The Validation Master Plan should define validation activities and outline responsibilities for authoring, reviewing, approving, and executing validation documentation and tasks. As an overview document, the Validation Master Plan should be clear and concise, not going into specific detail.
The Validation program must ensure policies and procedures comply with current Good Manufacturing Practices (cGMP). Systems such as calibration, preventative maintenance, change control, and revalidation contribute to a continuous state of validation.
Steps to follow to write a Validation Master Plan that meets Food and Drug (FDA) requirements include:
- Itemize the facilities, systems, equipment, and processes covered by the Validation Master Plan (e.g., systems, equipment, methods, facilities)
- Articulate the validation strategy and status of facilities, systems, equipment, and processes
- Define the change control processes to be followed
- Develop a plan and schedule for all validation and revalidation activities
- Secure approval from key stakeholders and management
- Remember to consider the various audiences (e.g., the quality, engineering, and regulatory departments, the FDA, outside contractors). Each group has different interests and requirements
- In-house teams need an accurate representation of systems and internal policies
- The FDA requires the pre-approved intention to comply with Federal regulations
- Outside contractors need a deliverables list to use to define the scope of work and develop proposals
Facilitate FDA Inspections with a Validation Master Plan
Title 21 Code of Federal Regulation Parts 11, 210, 211, and 820 set forth the FDA’s requirements for documentation to present an overall picture of the company facility, organization, and capabilities as well as an overview of how applicable cGMP.
While a Validation Master plan is not explicitly required, it provides a useful framework for creating the documentation required by the FDA, outlining the validation approach, strategy, and rationale involved in the further and pending qualifications. In addition to helping with documentation requirements, a Validation Master plan contributes substantially to assuring a quality product.
Egnyte has experts ready to answer your questions. For more than a decade, Egnyte has helped more than 16,000 customers with millions of customers worldwide.
Last Updated: 9th March, 2022
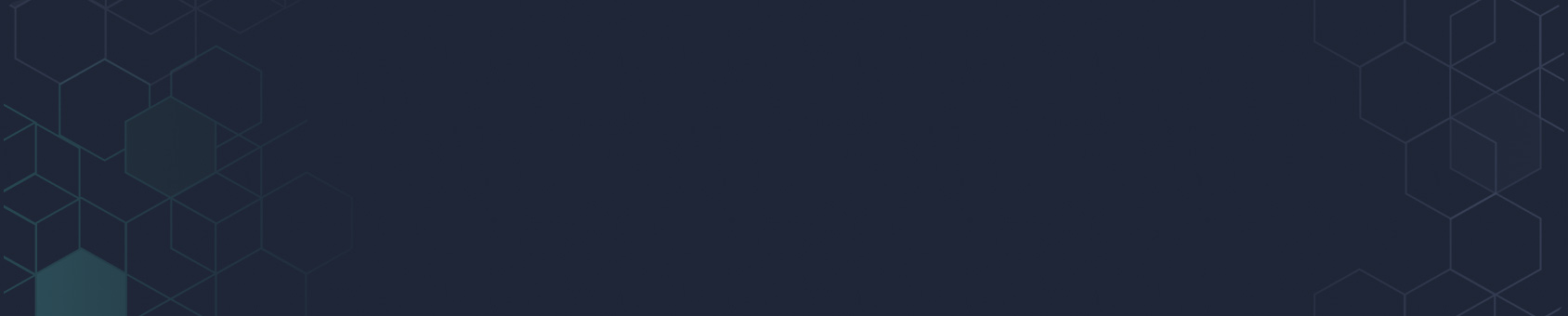